Laser Hardening – How Does it Work and What are the Advantages?
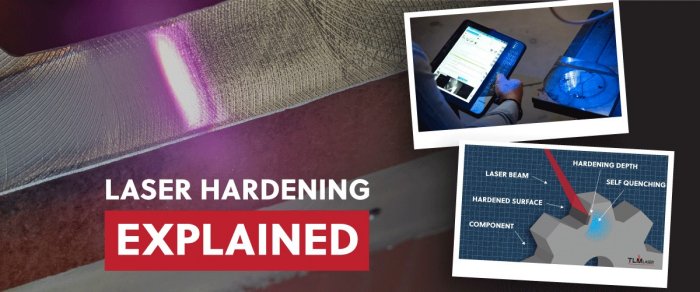
In the intricate landscape of manufacturing, the durability and reliability of components often dictate the performance and longevity of the final product. Many components face harsh operating conditions such as abrasion, impact, and wear during their service life. Without adequate protection, these surfaces are susceptible to premature failure, leading to costly downtime, maintenance, and replacement.
Surface hardening, therefore, becomes imperative to fortify these vulnerable areas, enhancing their resistance to wear, fatigue, and deformation. By equipping components with superior hardness and toughness, manufacturers can ensure optimal performance, extended service life, and ultimately, enhanced customer satisfaction. Thus, surface hardening emerges not merely as a process, but as a fundamental pillar of modern manufacturing, where strength, reliability, and longevity reign supreme.
However, it is important to understand how this process works and what are its advantages when compared to other methods.
Laser Hardening – The Science Behind the Process
The process of laser hardening begins with a high-powered laser beam being precisely directed onto the surface of a metal component. The intense energy of the laser rapidly heats the targeted area, surpassing the material's transformation temperature.
As the surface reaches the desired temperature, a phase transformation occurs within the metal. The structure changes to austenite, a high-temperature phase that exhibits greater ductility.
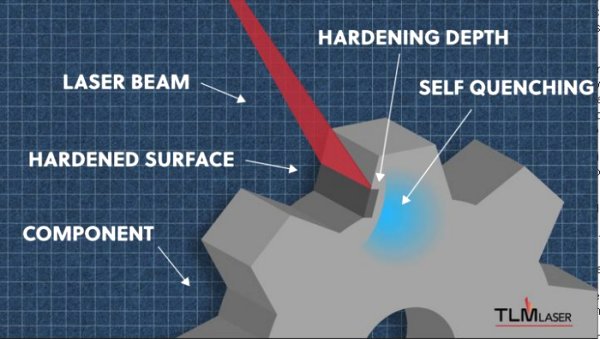
Following the heating phase, the surface is rapidly cooled, most other methods will use a quenching medium such as water or oil but with lasers there is no need for this as the workpiece rapidly cools itself, also known as “self-quenching”. This cooling stage transforms the surface structure into hard martensite, resulting in a completely hardened surface.
Through this meticulously orchestrated process, laser hardening achieves precise control over the depth and distribution of hardness, effectively bolstering the durability and longevity of metal components.
Laser Hardening – The Advantages
In the world of surface hardening there are many techniques but few that offer advantages in the same way lasers do. Providing unparalleled benefits in precision and speed is something which other techniques are not capable of. Here are some compelling reasons why laser hardening stands out:
- Precision and Control: Laser hardening enables precise modulation of heat input and hardening depth, ensuring targeted treatment with minimal risk of over-treatment or distortion.
- Complex Working: High-end systems such as the Alpha Laser AL-ROCK also offer 3D surface scanning, generating precise 3D models of the workpiece. Meaning not only does it offer maximum precision but also the ability to work to complex contours, edges, nubs and grain textures.
- Minimal Distortion: Unlike conventional methods like flame or induction hardening, laser hardening induces minimal distortion, making it ideal for components with complex geometries or tight tolerances.
- Selective Treatment: Laser hardening allows for selective treatment of specific areas, optimising material usage and reducing processing time.
- High Heating Rates: With its ability to achieve rapid heating rates, laser hardening enhances productivity and reduces manufacturing cycles.
- No Contact Required: Laser hardening operates without physical contact, minimising the risk of contamination and tool wear.
- Versatility: Laser hardening is compatible with a wide range of metallic materials, offering versatility across various industries and applications.
- Environmental Sustainability: By eliminating the need for quenching oils and chemicals, laser hardening reduces environmental impact and promotes sustainability.
There are a wide variety of UK Manufacturing businesses benefiting from laser hardening. One Alpha Laser customer noted that laser hardening reduced energy consumption by up to 95%. Another customer found great value in the speed processing benefits as their old method of vacuum hardening would take between 3-4 days, whereas using an Alpha Laser system they achieved more accurate results in just 23 seconds!
The AL-ROCK – The Laser Hardening ‘ROCK’star
Alpha Laser who manufactures the AL-ROCK laser hardening system, is the industry leader for laser hardening and welding machinery. The AL-ROCK Mobile is not your ordinary laser hardening tool however, equipped with a 4 kW laser, this innovative system is designed for surface metal hardening along with 6 additional processes. The AL-ROCK is equipped for:
- Hardening with scanner optics
- Wire deposition welding
- Wobble welding
- Deep welding
- Powder deposition welding
- 3D printing
- Pulse welding
In addition to its 7 in 1 process capabilities, what sets this system apart is its mobility - all essential components, including the laser, cooler, and robot controller, are seamlessly integrated into the robot chassis. This eliminates the hassle of transporting bulky control cabinets and accessories, making it truly portable.
With its self-propelled caterpillar track, the AL-ROCK Mobil can be easily manoeuvred to any location, whether at a customer's site or within a workshop. Gone are the days of dismantling components for processing; now, the laser can be brought directly to the workpiece, slashing setup time and reducing the need for rework. The best part? The system is ready for action within just 5 minutes, ensuring minimal downtime.
Watch the Alpha Laser AL-ROCK video below to get a true sense of this machine’s excellence.
If you think laser hardening could benefit your business and you would like to hear more about our Alpha Laser range then, please reach us on sales@tlm-laser.com or call us on 01527 959 099.
Other related articles: Press and Mould Tool Hardening