
Talk to Us!
Connect with our Technical & Support Team.

Key Feature
Tool & Die Hardening
Laser hardening significantly enhances the longevity and performance of tools and dies by creating wear-resistant surfaces. This precise process ensures extended tool life, reduced maintenance costs, and improved efficiency for demanding industrial applications.

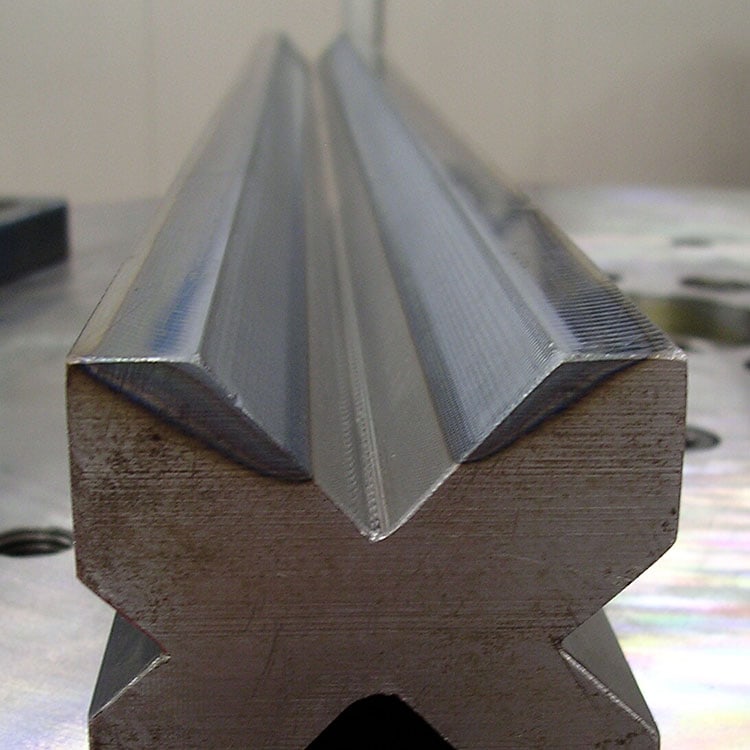
Information About Laser Hardening
Laser hardening as an application works by rapidly heating the metal surface using a focused laser beam, followed by controlled cooling. This process transforms the microstructure of the metal, creating a hardened layer while preserving the core’s toughness. Unlike traditional hardening methods, laser hardening targets only the required areas, reducing material distortion and enhancing precision.
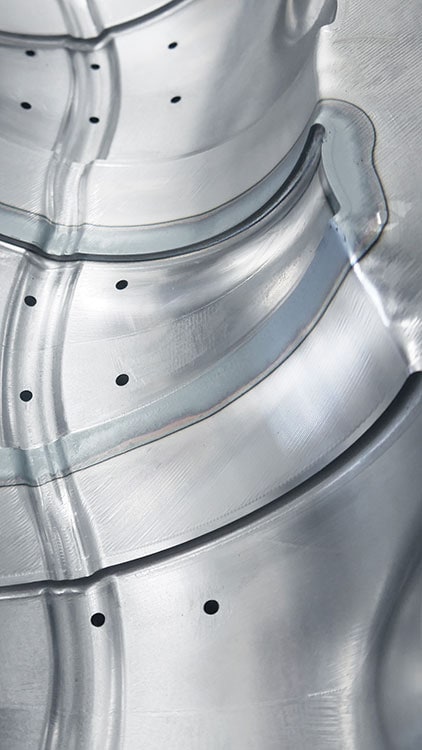
Laser Hardening for UK Industries
Laser hardening provides tailored solutions for industries requiring durable and wear-resistant components, ensuring superior performance under demanding conditions.
Harden critical components to withstand extreme operating environments and extend service life.
Improve the durability of gears, shafts, and other high-stress parts for enhanced performance.
Strengthen machinery components to reduce wear and minimise maintenance.
Enhance the lifespan of heavy-duty tools and structural components.
Extend the longevity of tools and dies, ensuring consistent performance and reduced downtime.
Harden equipment to resist wear and corrosion in harsh operating conditions.
Improve the durability of components used in renewable and conventional energy systems.
Strengthen rail components to withstand high loads and prolonged use.
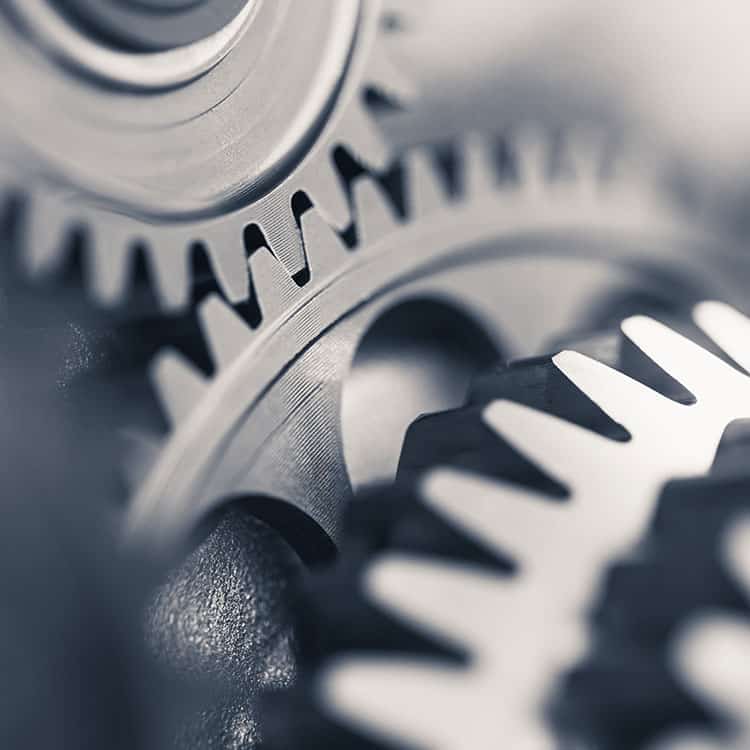
Laser Hardening Materials
Laser hardening is a versatile solution for enhancing the surface properties of various metals, delivering increased strength and durability.
Achieve precise, localised hardening on a wide range of metals, including steel and cast iron, for tailored performance improvements.
Answering Your Questions
Frequently Asked Questions
Laser hardening is primarily applied to ferrous metals, including various steels and cast irons, that have sufficient carbon content to undergo martensitic transformation. Industries such as automotive, aerospace and mechanical engineering utilise laser hardening to enhance the wear resistance and lifespan of components like gears, camshafts, and moulds. The process is particularly advantageous for large or complex parts, as mobile laser hardening systems can treat these components in situ, reducing downtime and eliminating the need for disassembly.
Laser hardening offers several benefits compared to conventional techniques:
- Precision and Control: The laser allows for exact control over the area being hardened, enabling selective treatment of specific surfaces without affecting the entire component.
- Minimal Distortion: Due to localised heating and rapid self-quenching, there is reduced thermal distortion, preserving the component’s dimensional accuracy.
- No Need for External Quenching: The process utilises the material’s own mass to cool the heated area, eliminating the requirement for external quenching media like water or oil.
- Efficiency: Laser hardening is a fast process, often completed in seconds, leading to significant time and energy savings.
Laser hardening is a surface treatment process that uses a high-powered laser beam to heat the surface layer of a metal component to its austenitizing temperature. This rapid, localised heating is followed by self-quenching, where the surrounding material cools the heated area quickly, transforming it into martensite—a hard and wear-resistant microstructure. This method enhances the surface hardness and durability of metal parts without the need for external quenching media.
Reviews
Don’t Just Take Our Word for It
Our Customers
Blog Posts
Laser News & Information

Talk to Us!
Connect with our Technical & Support Team.