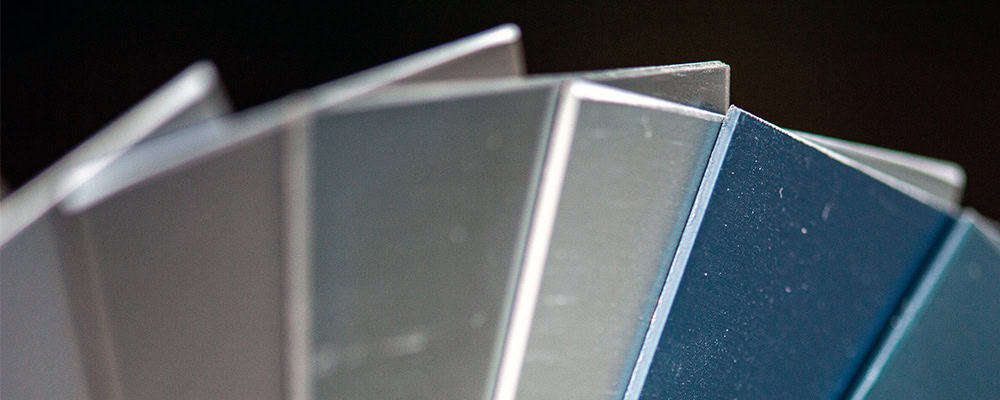
Metal
Lasers have revolutionised the way metals are processed in modern industries, offering unparalleled precision, speed, and versatility. From cutting, welding, marking, cladding and even additive manufacturing (3D printing), laser technology enables manufacturers to achieve high-quality results.
Fibre lasers, Nd:YAG lasers, and CO2 lasers are among the most commonly used systems for metal laser processing, capable of handling a wide range of applications such as creating intricate designs, joining dissimilar materials, or enhancing surface properties. Whether in aerospace, automotive, or industrial manufacturing, lasers have become an indispensable tool for working with metals like aluminium, stainless steel, titanium, and copper.
Laser technology is driving sustainability in metal fabrication by reducing material waste while delivering precise results. As industries strive towards greener practices, laser systems are leading the charge in sustainable manufacturing, lasers offer eco-friendly solutions for modern industries, whether it’s laser cutting lightweight aluminium sheets for electric vehicles or cladding turbine blades to extend their lifespan, fibre lasers ensure efficient use of energy during cutting and welding tasks with minimal environmental impact.
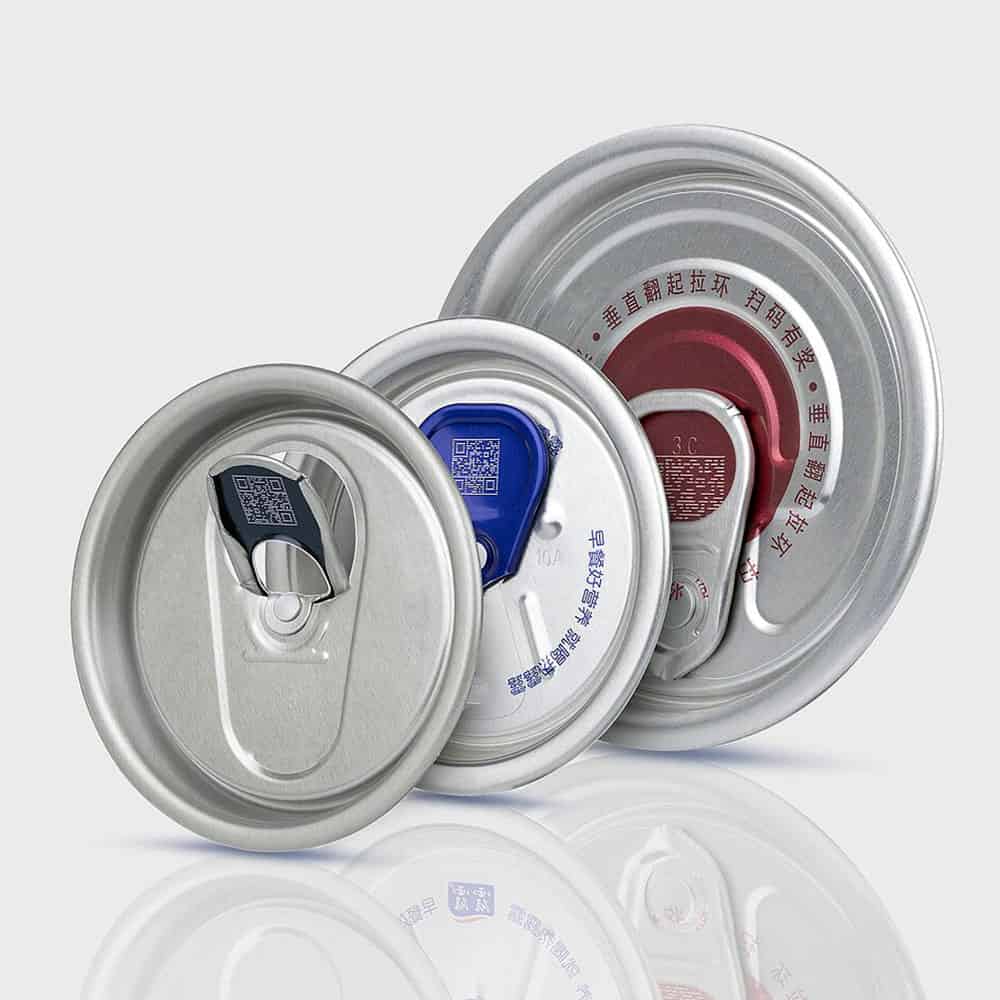
Corrosion-Resistant Marking for Durable Components in Manufacturing
TLM Laser supplies marking and engraving systems designed to deliver permanent, high-contrast marks on metals. Whether for traceability codes, logos, or intricate designs, our solutions ensure clarity and compliance with industry standards.
Our collaboration with FOBA guarantees superior results on metals such as steel, aluminium, titanium, copper, brass, gold and silver. With the ability to produce marks that resist wear, corrosion, and extreme conditions, these systems are ideal for aerospace, automotive, and medical applications. Laser engraving offers depth and detail, making it a preferred method for customisation or decorative elements.

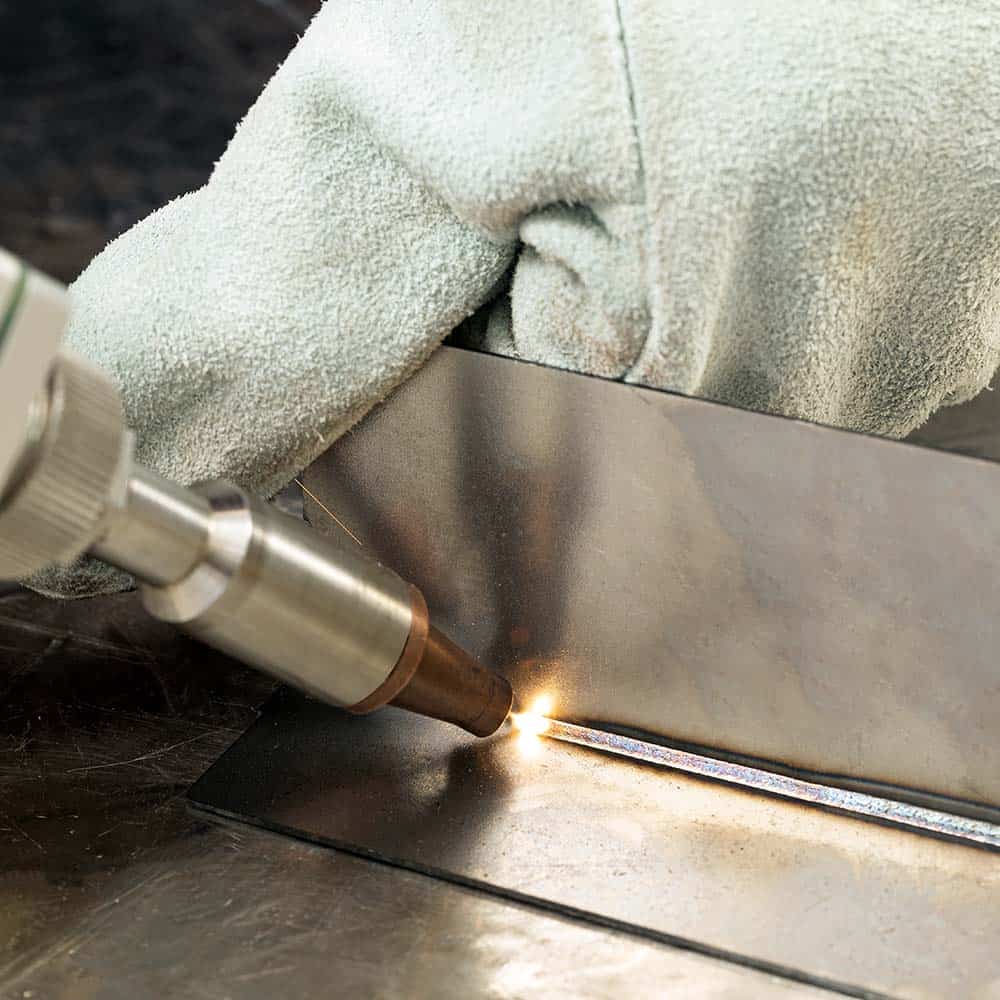
Welding High-Strength Metal Materials for Robust Assemblies
Laser welding has revolutionised metal joining, offering unparalleled precision and versatility across a wide spectrum of materials. TLM Laser’s advanced systems, powered by high-energy lasers, create strong, clean welds with minimal heat input, preserving the integrity of base materials. Our solutions excel in producing durable, low-distortion welds on stainless steel, aluminium, and other metals, making them ideal for demanding applications across industries.
Transforming Industries: From Automotive to Electronics
In automotive manufacturing, our laser welding technology enables the production of lightweight yet robust vehicle structures, combining different metal materials for optimal performance. From assembling complex engine components to fabricating structural parts, our systems ensure precision and efficiency. The aerospace sector benefits from our high-strength joints in critical components, while electronics manufacturers rely on our technology for joining delicate parts.
Our laser welding systems, developed in partnership with industry leaders like Alpha Laser and IPGs LightWELD, offer remarkable versatility. They can achieve narrow weld widths for microelectronics, and handle fabrication welding up to 4mm thick. This range allows us to cater to diverse needs, from micron-level precision to larger-scale industrial applications.
Whether you’re in automotive, aerospace, electronics, or general manufacturing, TLM Laser’s welding systems are tailored to meet the unique demands of your production line, ensuring superior quality and efficiency in metal joining processes.
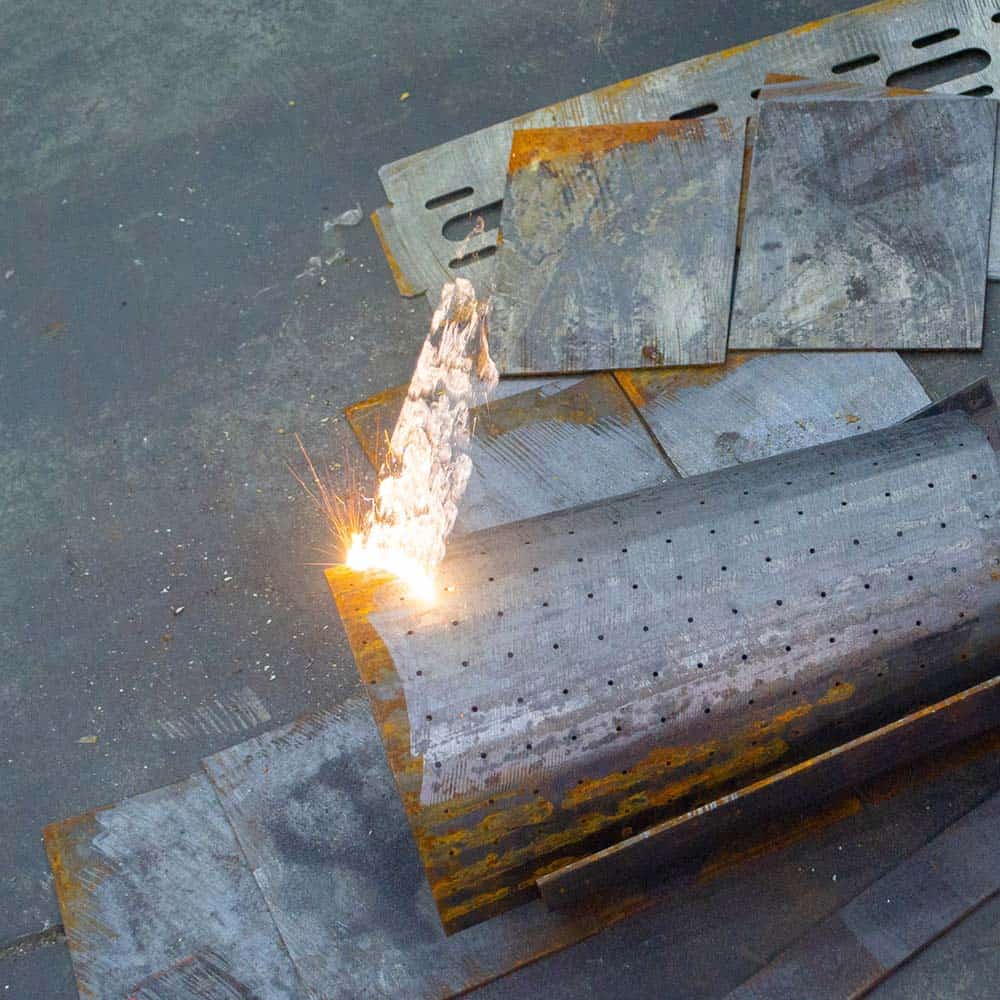
Preparing Metal Materials: Rust, Paint, and Contaminant Removal
TLM Laser provides advanced cleaning systems that remove rust, oxides, coatings, and contaminants from metal surfaces. This non-abrasive, chemical-free process helps restore and prepare metals for painting, welding, or extending mould lifecycles, reducing the need for traditional abrasive methods.
In collaboration with 4JET, our systems are designed for precision and reliability, offering unparalleled results for applications such as tool and mould maintenance, production line cleaning, and surface preparation.

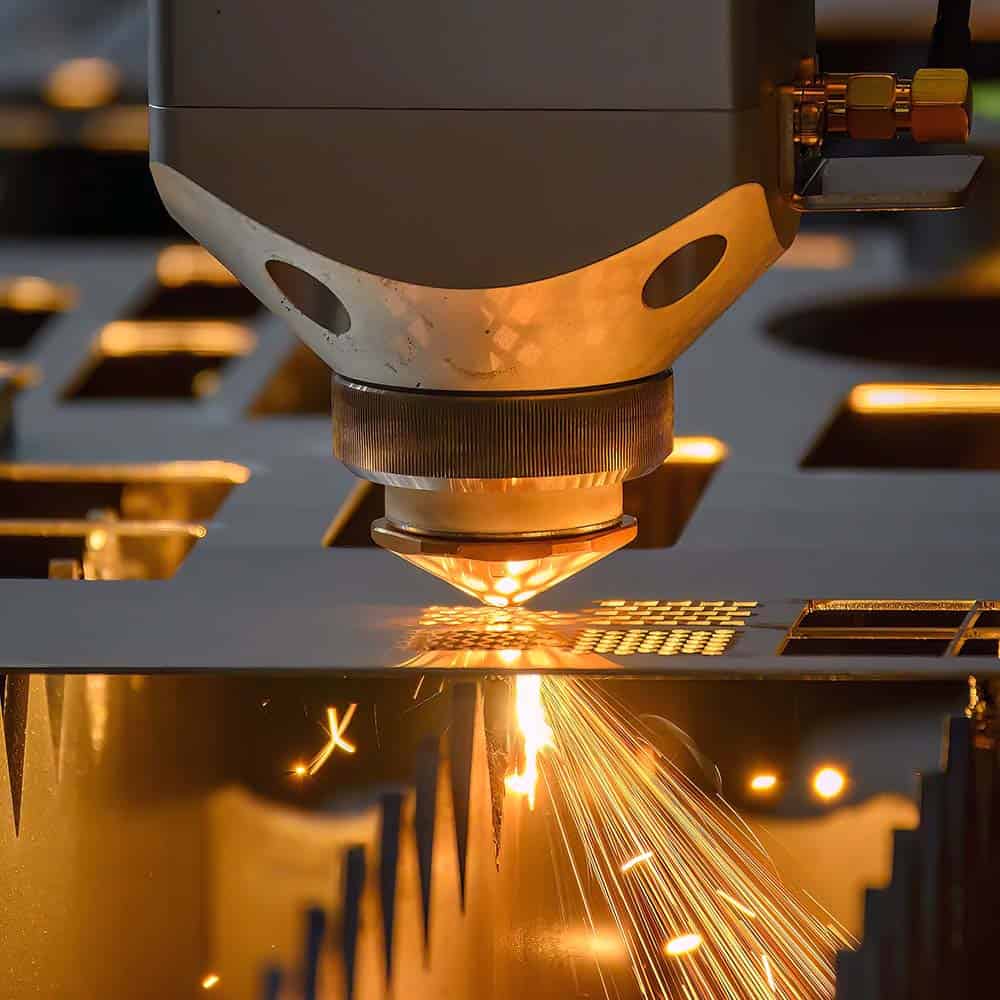
Intricate Cutting for Complex Metal Fabrication
TLM Laser’s cutting systems enable manufacturers to produce intricate and high-quality metal components with minimal waste. Whether working with stainless steel, aluminium, or alloys, our solutions offer clean cuts, high repeatability, and reduced processing times.
With support from Accurl and Universal Laser Systems, our cutting solutions cater to industries such as automotive, industrial machinery, and energy. These systems are ideal for both small-batch and large-scale production, delivering consistent results that meet stringent quality standards.
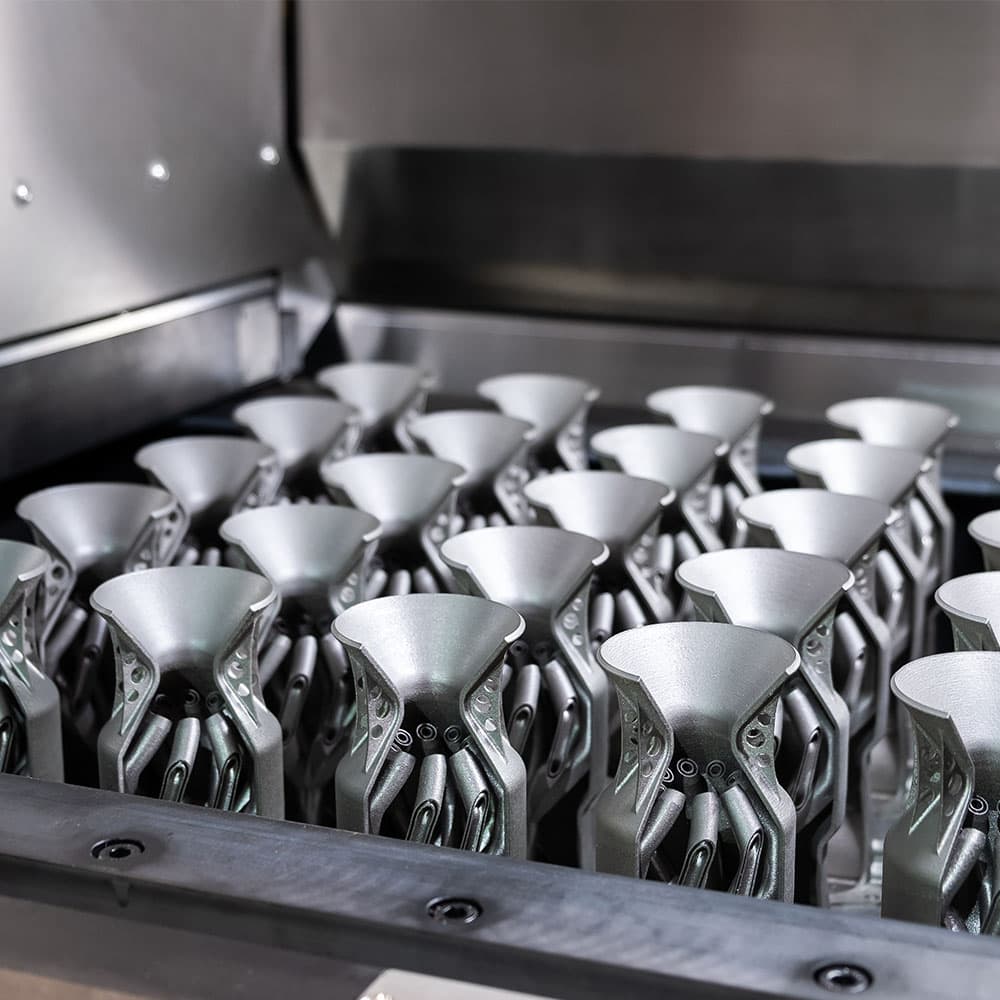
Innovating with laser-based 3D metal printing
The Power of Lasers & Metal 3D Printing
Laser-based metal 3D printing, including processes like Direct Metal Laser Sintering (DMLS) and Selective Laser Melting (SLM), is transforming manufacturing across industries. High-powered lasers fuse metal powders to create complex, functional parts directly from CAD models. This technology enables the production of lightweight, intricate components for aerospace, automotive, medical, and toolmaking applications. Key advantages include design freedom, sustainability, customisation, and faster production cycles.
Innovate with Confidence
Laser Machines and Systems
Reviews
Don’t Just Take Our Word for It
Our Customers

Talk to Us!
Connect with our Technical & Support Team.